کالیبراسیون دستگاههای تزریق کفشی و نقش آن در کیفیت زیره کفش
به گزارش اخبار صنعت چرم و کفش، کالیبراسیون دستگاه تزریق پلییورتان زیره کفش، با یک مواد خاص ثابت نیست. حتی در طول زمان و بدون تغییر مواد نیز امکان به هم خوردن کالیبراسیون دستگاه وجود دارد. لذا برای تولید زیره و کفش با کیفیت خوب و یکنواخت اکیدا پیشنهاد میشود:
با تغییر نوع و برند پلییورتان زیره کفش، کالیبراسیون دستگاه مجددا انجام شود.
حتی بدون تغییر نوع برند پلییورتان زیره کفش حداقل ماهی یک مرتبه کالیبراسیون انجام شود.
با تعویض پمپ مواد، تعویض هد دستگاه و شیلنگهای رفت و برگشت مواد، باید کالیبراسیون انجام شود.
دو نوع کالیبراسیون در دستگاه تزریق زیره کفش وجود دارد و انجام هر دوی این موارد همراه با هم الزامی میباشد:
کالیبراسیون نسبت واقعی ایزو به پلی
کالیبراسیون وزن تزریقی در زیره
تصور کنیم نسبت ایزو به پلی در دستگاهی 96 به 100 است (ایزو 96 و پلی 100) و در دستگاه دیگری با همان مواد نسبت ایزو به پلی 92 به 100 است (ایزو 92 و پلی 100) چرا یک نوع مواد (برند) در دستگاههای مختلف نسبت ایزو به پلی متفاوتی دارد؟ آیا مواد مشکل دارد یا دستگاه؟
در واقع نسبت ایزو به پلی این مواد با هر دو دستگاه (دستگاه اول 96) و (دستگاه دوم 92) صحیح است. پس سئوال اینجاست که چرا نسبتها در دستگاههای مختلف متفاوت است؟ برای پاسخ به این سئوال باید در باب اهمیت و نحوه عملکرد کالیبراسیون دستگاه اطلاعات کافی داشته باشیم.
1-کالیبراسیون نسبت واقعی ایزو به پلی
باید در نظر بگیریم که تعیین درست نسبت ایزو به پلی بر روی دستگاه و تولید یک زیره باکیفیت مناسب، ارتباط مستقیم با کالیبراسیون دستگاه دارد. دلایل لزوم کالیبراسیون نسبت واقعی ایزو به پلی:
1-1 مواد پلییورتان زیره کفش
مواد مختلف تولید شده در شرکتهای پلییورتانی (برندهای متفاوت) داری غلظت (ویسکوزیته یا گرانروی) مختلف میباشد.
2-1 دستگاه
دستگاههای ساخته شده در شرکتهای دستگاهسازی، به دلایل زیر میتوانند در تغییر نسبت ایزو به پلی موثر باشند.
قدرت الکترو موتور
حجم و دور پمپ
سایز و طول شیلنگهای رفت و برگشت
3-1 عوامل محیطی و اپراتور
عوامل زیر به دلیل تاثیر در گرانروی و حرکت مواد از درون تانک دستگاه تا سر هد و برگشت آن در تعیین صحیح نسبت ایزو به پلی موثر میباشند.
گرفتگی در قطر داخلی شیلنگهای رفت و برگشت
گرفتگی فیلترها
گرفتگی در قسمت شبکهای پمپها
گرفتگی در هد دستگاه
دمای محیط
دمای مواد درون تانک و شیلنگ دستگاه
توجه کنید که در یک تزریق، مواد در سر هد حتما باید با هم خارج شوند و با هم قطع گردند اگر دور پمپها به درستی تنظیم نباشند باعث خروج بیش از حد یک جز نسبت به دیگری (پلی یا ایزو) شده و در نتیجه نسبت ایزو به پلی تغییر میکند. در این موارد باید به منوی کالیبراسیون دستگاه رجوع شود و کالیبراسیون با شرح زیر انجام گردد:
برای کالیبراسیون دستگاه دو روش وجود دارد؛ در روش اول باید در یک دور پمپ ثابت و زمان ریزش ثابت، خروجی مواد به صورت جدا (ایزو و پلی) وزن گرفته شود و در قسمت تعین شده در منوی کالیبراسیون دستگاه وارد گردد. با این کار دور پمپها به صورت اتوماتیک تنظیم میشود. حال با خروج از منوی کالیبراسیون و قراردادن نسبت ایزو به پلی 100 به 100 در منوی دستگاه مجددا از خروجی سر هد مواد را جدا جدا گرفته و وزن میکنیم. باید هر دو وزن ایزو و پلی در این مرحله مساوی باشد در غیر از این حالت باید عمل کالیبراسیون تکرار شود تا وزن پلی و ایزو برابر گردد.
در روش کالیبراسیون دوم، به جای وارد کردن وزن مواد ایزو و پلی در منو کالیبراسیون دستگاه، وزن مواد ایزو را بر وزن مواد پلی تقسیم میکنیم که باید حاصل تقسیم با نسبت قرار داده شده درون دستگاه برابر باشد در غیر این صورت باید دور پمپ مورد نظر را تغییر داد و این کار را آنقدر تکرار کرد تا نسبت واقعی به دست آمده از طریق وزن مواد با نسبت قرار داده شده در منوی دستگاه برابر شود.
2- کالیبراسیون وزن
یکی از تستهای متداول این دستگاهها که به صورت روتین توسط اپراتورها انجام میشود بدین صورت است که دو لیوان را در زیر هد قرار میدهند و مواد ایزو و پلی خروجی را به صورت مجزا میگیرند سپس با تقسیم آنها بر هم میبینند که آیا نسبت به دست آمده به نسبت تعیین شده بر روی دستگاه یکی است یا خیر. باید گفت این تست اشتباه نیست اما کامل هم نیست چرا که با تغییر مواد و تغییر غلظت آن مواد خروجی از سر هد متفاوت خواهد بود در نتیجه میزان وزن نهایی و به تبع آن دانسیته زیره متفاوت خواهد بود و اینجاست که ممکن است زیره تولیدی بعد از مدتی دچار جمع شدگی شود. توجه کنید که در این حالت هم مواد کیفیت مطلوب را داردهم نسبت درست ایزو به پلی وجود دارد هم دستگاه سالم است و تست خطی را به درستی نشان میدهد اما باز هم ما جمع شدگی در زیره را شاهد هستیم. مشکل کجاست؟ برای پاسخ به این سئوال باید ابتدا وزن زیره تولید شده را مورد بررسی قرار دهید. اگر زیره را بر روی ترازو قرار دهید و بررسی کنید آیا وزن زیره با وزن بر روی دستگاه برابر است یا خیر؟ خواهید دید که این طور نیست و شاهد وزن کمتری (دانیسته زیره پایینتر) به نسبت وزن ورودی در منوی دستگاه هستید! این امر معمولا زمانی اتفاق میافتد که کالیبره دستگاه را بر روی یک نوع مواد با غلظت خاص انجام دادهاید و اکنون درصدد استفاده از ماده جدیدی از شرکت دیگری (برند متفاوت) هستید.
مواد تولید شده در شرکتهای مختلف دارای غلظتهای متفاوتی هستند و این امر باعث میشود با یک دور ثابت از پمپ، وزن خاصی از مواد از هد خارج شود. برای مثال تصور کنید که دور پمپ بر روی 4000 دور بر دقیقه ثابت باشد، سپس عمل کالیبراسیون را انجامدهید؛ به این صورت که وزن مواد خروجی از سر هد را به دستگاه بدهید (برای مثال در یک ثانیه 30 گرم مواد از سر هد با دور 4000 خارج شده است) حال نوع مواد را تغییر دهید و موادی با غلظت بالاتر را جایگزین کنید و دوباره کالیبراسیون را تکرار کنید. خواهید دید که با دور پمپ 4000 در زمان یک ثانیه 20 گرم مواد از سر هد خارج شده است. این تفاوت به دلیل غلظت مواد شماره 2 نسبت به یک میباشد. همین امر در هنگام تزریق درون قالب هم رخ میدهد و وزن نهایی زیره با مواد با غلظت بالاتر کمتر و زیره سبکتر میشود (دانسیته زیره پایینتر خواهد بود). پس لازمه کار این است که دور پمپ به نسبت غلظت مواد تغییر کند (مواد با غلظت پایین دور پمپ پایین و مواد با غلظت بالا دور پمپ بالا نیاز خواهد داشت) برای این امر باید کالیبراسیون وزن انجام داد که انجام آن در دستگاههای مختلف متفاوت است و باید با سازنده دستگاه برای این تنظیمات مشورت کنید.
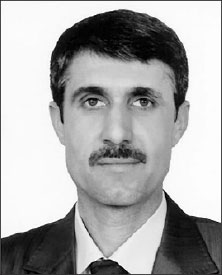
تالیف: رمضان حسنپور
کارشناس ارشد فروش، تولید و خدمات فنی مواد پلی یورتان کفش